Tianjin Botai Heat Exchange Equipment Co.,Ltd
Reasons for excessive pressure drop in plate heat exchangers
2020-03-06
When selecting the area of the plate heat exchanger for the first time, if it is too small and the system piping has not been properly flushed, excessive pressure drop may occur during use.
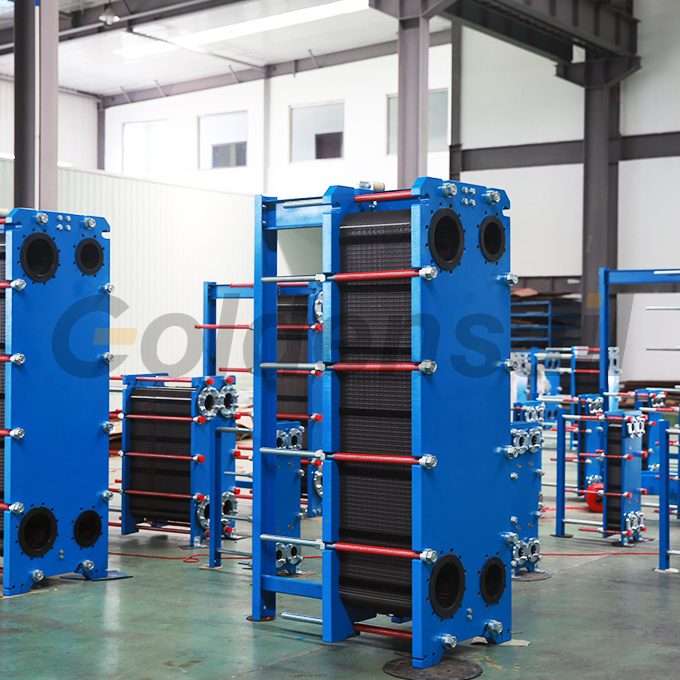
Causes:
1. The area of the plate heat exchanger was too small during the initial selection, resulting in excessively high flow rates between the plates and increased pressure drop.
The operating system piping was not properly flushed, especially with many contaminants (such as welding slag) entering the interior of the plate heat exchanger in newly installed system piping. Due to the narrow cross-sectional area of the flow channels in the plate heat exchanger, sediments and suspended solids accumulate at the corner holes and in the flow guiding area, significantly reducing the flow channel area at these points, leading to major pressure losses in this area.
2. The operating system piping was not properly flushed, especially with many contaminants (such as welding slag) entering the interior of the plate heat exchanger in newly installed system piping. Due to the narrow cross-sectional area of the flow channels in the plate heat exchanger, sediments and suspended solids accumulate at the corner holes and in the flow guiding area, significantly reducing the flow channel area at these points, leading to major pressure losses in this area.
3. After the plate heat exchanger has been in operation for a period of time, excessive pressure drop occurs due to scaling on the surface of the plates.
Treatment methods:
1. Remove contaminants or scale from the flow channels of the heat exchanger. For newly operated systems, clean once a week based on actual conditions. When cleaning the scale (mainly referring to CaCO3) from the surface of the plates, use a cleaning solution containing 0.3% amino sulfonic acid solution or a solution containing 0.3% urotropine, 0.2% aniline, and 0.1% potassium thiocyanate in 0.8% nitric acid, with a cleaning temperature of 40 to 60°C. When performing chemical immersion cleaning without disassembling the equipment, open the inlet and outlet of the heat exchanger for the cold medium, or install a DN25 cleaning port on the inlet and outlet pipes during installation, inject the prepared cleaning solution into the equipment, soak, and then rinse with clean water to remove residual acid, ensuring pH ≥ 7. When disassembling for cleaning, soak the plates in the cleaning solution for 30 minutes, then gently scrub the scale with a soft brush, and finally rinse thoroughly with clean water. During the cleaning process, avoid damaging the plates and rubber gaskets. If using a non-disassembly mechanical backwashing method, connect a pipe to the inlet and outlet piping of the medium in advance, connect the equipment to the mechanical cleaning vehicle, and inject the cleaning solution in the reverse direction of the medium flow, with a circulation cleaning time of 10 to 15 minutes, controlling the medium flow rate at 0.05 to 0.15 m/s. Finally, rinse several times with clean water, ensuring that the Cl mass concentration in the clean water is controlled below 25 mg/I.
2. The secondary circulating water should preferably use softened water that has been treated, generally requiring that the mass concentration of suspended solids in the water does not exceed 5 mg/L, the diameter of impurities does not exceed 3 mm, and pH ≥ 7. When the water temperature does not exceed 95°C, the concentrations of Ca and Mg should not exceed 2 mmol/L; when the water temperature exceeds 95°C, the concentrations of Ca and Mg should not exceed 0.3 mmol/L, and the mass concentration of dissolved oxygen should not exceed 0.1 mg/L.
3. For centralized heating systems, a method of one-time replenishment to the secondary water can be used.
Previous Page: